The significance of friction testing
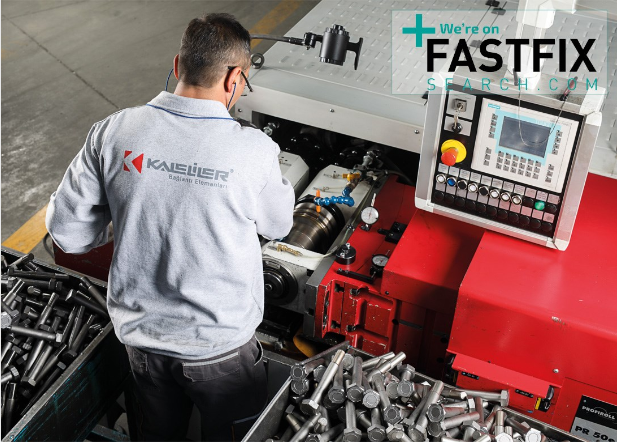
Kaleliler has further invested in its in-house laboratory with the introduction of a new friction testing machine. Here the Turkish manufacturer explains the role of friction testing within the fastener industry and how the new machine will enable it to perform tests across its complete range of bolting sets.
Fasteners are essential components used to hold objects together – coming in different shapes and sizes and used in various applications, such as in the automotive and aerospace industries, as well as in construction
and manufacturing.
One critical aspect of fastener design and production is the ability to resist the forces of friction, with a friction test a standard method used to evaluate the performance of fasteners in resisting frictional forces.
The friction test involves measuring the frictional force required to turn a threaded fastener when it is tightened to a specific torque. This test helps to determine the frictional characteristics of the fastener and the mating surfaces. It also helps to evaluate the performance of the lubricants used in the assembly process.
To perform the friction test, a torque measurement device is attached to the head of the fastener and a rotational force is applied to the fastener. The device records the torque required to turn the fastener, which is then used to calculate the coefficient of friction. The coefficient of friction is a ratio of the frictional force to the normal force between the fastener and the mating surface.
The friction test can be performed under dry or lubricated conditions. Dry friction tests involve tightening the fastener without any lubricant or coating, while lubricated tests involve the use of a specific lubricant or coating. The lubricant or coating can help to reduce the frictional forces and improve the fastener’s performance.
In addition to evaluating the frictional characteristics of fasteners, the friction test can also help to determine the optimal torque for a given fastener and mating surface combination. The optimal torque is the torque required to achieve the desired clamping force without exceeding the fastener’s yield strength. The yield strength is the point at which the fastener deforms permanently.
The friction test can also help to identify potential problems with the mating surfaces. For example, if the coefficient of friction is higher than expected, it could indicate that the mating surfaces are not flat or have rough spots that increase the frictional forces. Identifying these issues can help to improve the design and production processes, as well as ensure that the fasteners perform as expected.
In conclusion, the friction test is a critical method used to evaluate the performance of fasteners in resisting frictional forces. It helps to determine the frictional characteristics of the fastener, and mating surfaces, and identify potential issues with the design and production processes. By performing friction tests, engineers and manufacturers can improve the performance and reliability of their fasteners, leading to better products and safer applications.
Through its investment in a new friction testing machine Kaleliler Civata Sanayi ve Ticaret Anonim Sirketi will be able to perform tests on a whole range of bolts – from M12 to M72. The measuring capacity is from 500kN to 3,000kN and up to 30,000Nm with three full bridges of strain gauges and resolution of angle encoder of 0.1°. Kalelilier also ensures its tests are carried out to the relevant standards, with this test performed as described in EN14399-2, with three different size three-component sensors; each one able to measure clamping force, total torque and frictional torque under the bolt head – with accuracy class 0.5.
www.kaleliler.com.tr/en/home
Please first Loginlater ~